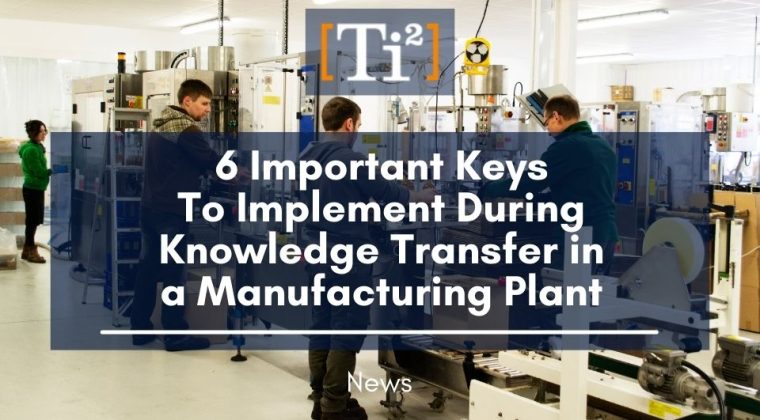
Implementing a new process or procedure in your manufacturing company can be challenging. After all, there are many different mechanisms involved and many moving parts. To make things even more difficult, not everyone’s aware of the need for the change—and some employees might even feel threatened by it. That’s why you have to approach the implementation differently than you do with other processes. Here are 6 important keys that you should keep in mind as you implement a new process during knowledge transfer in a manufacturing company.
Show, Don’t Tell
When you start adopting a new process in your company, you’re going to want to show your employees why this change is occurring and why it’s important. Be prepared to do this in person, over email, and/or over a document. Don’t hide the new process behind a curtain or under a bushel. Cast a bright light on the change so your employees can clearly see the benefits and see why they need to adopt it.
Be Realistic About Timing
Every manufacturing company has a different timeline for implementing a new process. The timing will be affected by a number of factors, such as how long the process is currently taking, how much it costs, and how many other processes are competing for resources. Your timing also depends on your employees’ knowledge level, their skill level, and their comfort level with the change.
Are they resistant to the change or are they ready for it? Keep in mind that some employees might get impatient during the knowledge transfer process. Their excitement to adopt the change might be swamped by their own impatience. To keep the knowledge transfer process from becoming a bottleneck, you need to be realistic about when each person receives the change and how soon they can start using it.
Be Flexible And Committed To Iteration
During the knowledge transfer process, you’ll want to be flexible with your timing and the introduction of the new process. You’ll also want to be flexible with the implementation of the new process. But don’t be too flexible. It’s a fine line to walk. Set proper boundaries and clearly set your authority of which variables are flexible and which are non-negotiable.
In order to successfully implement a change, you need to commit to the change and be committed to the change’s iteration. The best way to do this is to keep the knowledge transfer process flexible.
Pro-actively Communicate Change
During the knowledge transfer process, you need to proactively communicate the change. In the same way that you would communicate new process updates to employees, you need to communicate the change to your customers.
- Make sure you let your key customers know what’s happening and why.
- Make sure you let your key vendors know what’s happening and why.
- Make sure you let your key suppliers know what’s happening and why.
- Connect these key audiences with your process change.
Make sure they know that you’re changing your process, explain to them the reasons why you’re changing your process, and let them know that they can expect to see the change.
The more key audiences you pro-actively connect with, the better.
Create A “Haptic” Experience
During the knowledge transfer process, you need to create a “haptic” experience. Your employees and customers need to know what’s happening and why it’s happening. To create a “haptic” experience, communicate the change in person, over email, and/or over a document. The more forms of communication you use, the better. Ensure you include visual and aural cues, such as diagrams, images, and audio.
Establish A Formal Knowledge Transfer Program
During the knowledge transfer process, you need to establish a formal knowledge transfer program. You need to define what knowledge transfer is, how you’ll track the process, who will lead the knowledge transfer program, and who will lead each key knowledge transfer activity.
Knowledge transfer activities include training (or re-training), mentoring, transfer of authority, and transfer of responsibility.
Wrapping Up
When a new process is implemented in a manufacturing company, it can be challenging to implement during knowledge transfer in a manufacturing company. During knowledge transfer, you have to proactively communicate the change, create a “haptic” experience, establish a formal knowledge transfer program, and wrap up. To successfully implement a new process, you need to be flexible, realistic about timing, and committed to iteration. You need to be flexible and committed to a haptic experience as well throughout the knowledge transfer program.
Ti2 Pty Ltd offer a wide range of quality industrial automotive, automation, and information products and services. Using genuine open standards and technologies for industrial solutions we are able to reduce overall cost of ownership.
- Our complete turn-key solutions and specialised integration includes, but is not limited to:
Electrical and Software Design - Hardware/Software/Mechanical/Electrical integration
- Industrial Systems Programming (PLCs, HMI’s, soft PLCs, Robotics, Servo Controllers)
- Project Specification & Management
- Testing and Commissioning
As for R&D, we specialise in:
- R&D for new and existing products & processes, including medical and sport
- Automotive Diagnostics
- Test Rigs and Diagnostic units
- OPC and communication driver development
And lastly, to complete the full solution, we provide training and support through:
- Remote Access Support
- Operator & Maintenance Staff Training
- Focus on ‘open’ programming standards
- ‘IEC61131-3’ and OPC presenters
To learn more about what we do and how we can help your training and support requirements, please click projects, products & services.
Ti2 is currently very focused on working with its global partners to secure stock and avoid long delay times in delivering products to their customers. Together with our trusted partners, we are here to provide solutions.
Please click here to email us your inquiry, we would like to hear from you.