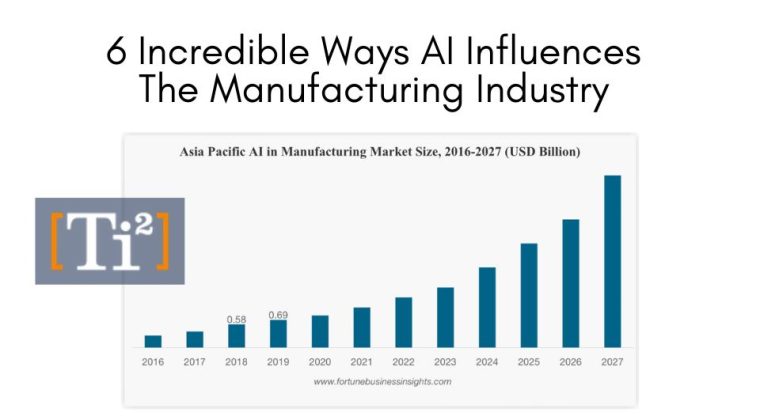
Do you remember the world before AI? Perhaps some of us… The silent generation, baby boomers, gen x, would know. But the younger generation, millennials, gen z, iGen, and centennials, definitely don’t.
Not only in our daily lives, but the use of AI (Artificial Intelligence) in manufacturing is also game-changing. It divides the industry into “before” and “after” phases.
According to Fortune Business Insights, AI in the manufacturing market size is estimated to reach $9.89 billion by 2027. Automotive, semiconductors, and medical devices manufacturing industries are expected to contribute significantly to the growth of the AI market.
Moreover, AI became a salvation for various companies that were impacted by Covid-19. AI technology allows companies to apply predictive analytics, analyse error possibilities in real-time, and optimise workload.
With AI, manufacturing plants can now:
- Detect defects throughout the pipeline and production process
- Schedule and implement predictive maintenance for less downtime
- Real-time visibility in demand across the supply chain
- Improve QC (quality control) process
- Bulk-batch production ability – fewer small-batches (cost-efficient and customisable)
- Elimination of tedious tasks (reduced human labor)
- Operate near-shore facilities using advanced manufacturing
The key uses of AI in manufacturing are the following:
Defect Detection: Time is money – With the help of computer vision operated by AI, time-saving is of the essence. AI identifies the damages and defects of products. It covers the role of human labor in improving the quality of inspection, where some defects may not be visible to the bare eyes.
Real-time data analytics saves time and improves the quality of the final product. Along with that, the collected data allows engineers to big data collection for further assembly line improvement and prevent future defects.
Many manufacturing companies have testified that AI has saved them money, and time, reduced waste, and improved the quality of products and production lines from an overall perspective.
Quality Assurance: Image processing algorithms have been a big help to the industry.
Quality assurance is now conducted automatically, in real-time, with less human error. Sourced from the BMW Group, the leading automotive company uses automated image recognition for quality checks, inspections, and to eliminate pseudo-defects (deviations from target despite no actual faults). The proven technology has yielded high levels of precision in manufacturing.
Assembly Line Integration: Modern IoT-connected equipment used in plants produces millions and billions of valid and important information. With AI, all cloud-stored data are organised, managed, and decluttered for the best use and measurement for future use.
Assembly Line Optimisation: With AI, monitoring and neutralising failure and damage are more preventative with real-time and predicting analysis. Collected data help optimise the production line and ensure the final quality improvement.
Generative Design: AI allows engineers to test alternative designs that are possibly deployed within the plant. This includes integration possibilities.
Broader Production Automation: A great example can be the Porsche company. They are applying autonomous guided vehicles (AGVs) that transfer vehicle body parts from one station to another without human help. That innovation was especially beneficial during the pandemic when lots of companies had to shut down due to the “new normal” regulations.
According to McKinsey, companies using AI have witnessed cost savings and revenue growth. 16% of those surveyed noticed a 10-19% decrease in costs, whereas 18% saw a 6-10% increase in overall revenue.
With predictive analysis, AI systems overcome challenges such as operational, supply chain, workforce, etc. A McKinsey report also suggests that AI can improve forecasting accuracy in manufacturing by 10-20%, which translates to a 5% reduction in inventory costs and a 2-3% increase in revenues.
According to the IFR (International Federation of Robotics), there were already 2.7 million industrial robots operating in factories worldwide in 2020. This was a 12% increase as compared to 2019, and with digitisation initiatives growing exponentially, the tendency is projected to grow further.
In conclusion, AI is strongly affecting the manufacturing industry and manufacturers will continue investing in AI technologies and machine learning to further reduce production costs and improve time-to-market. We are all striving to make businesses more resilient by automating tasks, forecasting disruptions, and facilitating end-to-end control.
To learn more about what we do and how we can help your interoperability requirements, please click projects, products & services.
Ti2 is currently very focused on working with its global partners to secure stock and avoid long delay times in delivering products to their customers. Together with our trusted partners, we are here to provide solutions.
Please click here to email us your inquiry, we would like to hear from you.
Article inspired by McKinsey, IFR, Fortune, and Ti2.