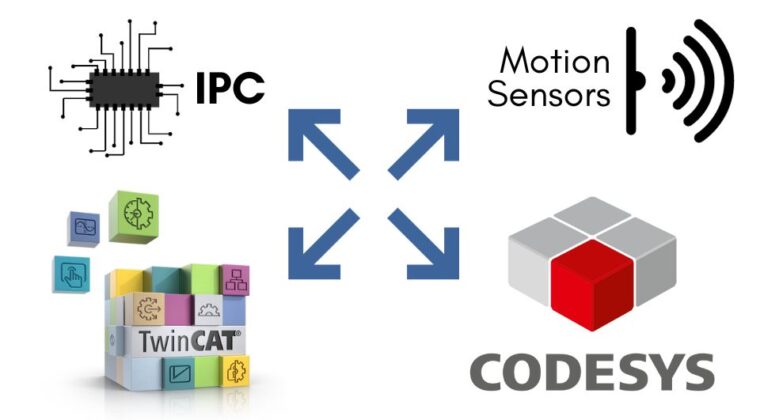
TwinCAT, CODESYS, IPCs, and Motion Sensors as Brains, Nervous System, Eyes and Ears. I wanted to make this blog slightly more interesting, and digest-able. The analogy is that:
- TwinCAT and CODESYS serve as the brain, providing the logic and control algorithms that govern the system’s behavior.
- IPCs act as the central nervous system, handling high-level computations, data processing, and communication between different components.
- Motion sensors provide crucial feedback to the system, enabling it to adjust and synchronise movements in real-time.
Engineers spanning disciplines such as automation, robotics, electrical, mechanical, and process engineering utilise TwinCAT, CODESYS, IPCs, and motion sensors in diverse industrial applications. Automation engineers employ TwinCAT and CODESYS to program PLCs and enhance control logic, while IPCs manage high-level computations. Robotics engineers integrate motion sensors for precise robotic movement. Electrical engineers interface sensors and control devices with TwinCAT and CODESYS, while mechanical engineers collaborate on mechanical integration. Process engineers optimise industrial processes using these tools. Students, researchers, and professionals in industrial automation find value in learning about these technologies, which are essential in modern automation systems, ensuring efficiency, safety, and precision in a wide range of industries.
The correlation between TwinCAT, CODESYS, IPCs, and motion sensors lies in their collaborative role within complex automation projects.
TwinCAT provides a comprehensive environment for tasks like motion control, PLC programming, and HMI development. Great to create the logic and control systems that govern the behavior of machines and processes. CODESYS serves a similar purpose to TwinCAT, providing a platform for developing control applications, many of the principles and techniques learned in TwinCAT are transferable to CODESYS, due to their shared roots.
However, there are some key differences between TwinCAT and CODESYS:
TwinCAT:
- Developed by Beckhoff Automation.
- Known for its real-time capabilities and high performance.
- Well-integrated with Beckhoff’s hardware, providing seamless compatibility.
- Offers advanced features for complex motion control applications.
CODESYS:
- CODESYS is a platform-independent development environment, which means it can be used with a wide range of PLC manufacturers.
- It is known for its user-friendly interface and strong community support.
- It’s a versatile tool that can work with various types of controllers.
As for making them work together, it is possible to integrate systems that use both TwinCAT and CODESYS. This could involve using communication protocols like OPC UA, Modbus, or others to facilitate data exchange between the two systems.
Ultimately, the decision between TwinCAT and CODESYS should be based on the specific requirements and constraints of your project, as well as the compatibility with your existing hardware and systems. Additionally, it’s worth consulting with an automation expert. Contact us to book a consultation call HERE.
IPCs
IPCs serve as the computing backbone, handling tasks such as centralised path generation, real-time data processing, and high-level coordination of subsystems. IPCs are essential for managing and orchestrating an automation system. One of their paramount strengths lies in real-time data processing, where their multi-core processors, high-speed memory, and optimised architecture facilitate rapid ingestion, processing, and dissemination of data. This capability proves invaluable in applications demanding split-second decision-making, such as in high-speed manufacturing lines or precision robotics.
In addition, IPCs boast advanced diagnostics tools that delve into the minutiae of system health. Through intricate monitoring of hardware parameters, thermals, and component statuses, IPCs provide engineers with a comprehensive overview of system performance. This, in turn, enables proactive maintenance, reducing downtime and averting potential system failures.
Furthermore, IPCs serve as the lynchpin for high-level coordination of disparate subsystems within complex automation setups. With support for a multitude of communication protocols, ranging from fieldbuses like EtherCAT to industrial Ethernet standards, IPCs facilitate seamless interconnectivity. They become the focal point for data aggregation, protocol conversion, and synchronisation of actions across PLCs, HMIs, motion controllers, and other devices. In effect, IPCs act as a centralised brain, orchestrating the symphony of activities across the automation landscape.
To put this into practical context, consider a highly integrated smart factory. Here, an IPC might oversee the synchronisation of robots, conveyors, vision systems, and inventory management. It processes real-time data streams from each subsystem, ensuring optimal resource allocation, adaptive scheduling, and rapid response to dynamic production demands. Through its advanced diagnostics, it can preemptively detect a failing component, triggering a maintenance alert before operations are compromised.
Motion Sensors
Motion sensors are the eyes and ears of an automation system. They provide real-time feedback about the movement and position of components. This information is crucial for ensuring precise control and synchronisation of movements, which is especially important in scenarios like robotics, where accuracy is paramount.
The integration of high-level vision systems with TwinCAT or CODESYS represents a quantum leap in the capabilities of automation, enabling complex real-time decision-making based on visual data. This convergence empowers automation systems to perform tasks traditionally reserved for human operators. Object recognition, a foundational task in this integration, allows the system to identify and categorise objects within its field of view. This capability extends to tracking, where the system can follow the movement of objects over time, enabling dynamic interactions in response to their positions.
Advanced vision algorithms form the crux of this integration. These algorithms underpin tasks such as pattern recognition, feature extraction, and spatial analysis. For instance, in a manufacturing environment, the system can utilise advanced algorithms to identify minute defects in products or accurately measure dimensions to ensure compliance with precise specifications. Such capabilities have transformative implications for quality control and process optimisation.
Case studies further illuminate the potential of this synergy. In a smart warehouse setting, high-level vision systems integrated with TwinCAT/CODESYS can facilitate autonomous inventory management. The system can recognise and track individual items, dynamically updating inventory levels in real time. This not only eliminates the need for manual stocktaking but also allows for proactive restocking and order fulfillment, optimising operational efficiency.
In another application, consider an automated inspection system for semiconductor manufacturing. By integrating advanced vision algorithms with TwinCAT/CODESYS, the system can identify microscopic defects on silicon wafers, ensuring only flawless components proceed to the next stage of production. The result is a dramatic increase in yield and a reduction in costly rejections.
Control Algorithms
Introducing control algorithms such as Model Predictive Control (MPC) and Adaptive Control Strategies represents a paradigm shift in the precision and adaptability of motion systems. MPC, for instance, is a dynamic optimisation technique that factors in system dynamics, constraints, and objectives to compute control inputs. This enables MPC to anticipate future system behavior, allowing for proactive adjustments that optimise performance. Adaptive control strategies, on the other hand, dynamically adjust control parameters based on real-time feedback, allowing the system to adapt to changing conditions and uncertainties.
Comparatively, these advanced algorithms offer distinct advantages over traditional Proportional-Integral-Derivative (PID) controllers, particularly in scenarios demanding intricate motion control. For instance, in scenarios with complex, non-linear dynamics or strict operational constraints, MPC shines. Its ability to consider future states and constraints allows it to navigate complex scenarios with finesse, ensuring optimal performance even in the face of dynamic changes.
In scenarios with uncertain or time-varying parameters, adaptive control strategies excel. Unlike PID controllers, which rely on fixed control gains, adaptive strategies continuously adjust control parameters based on real-time observations. This allows the system to maintain precise control even as conditions evolve, ensuring robust performance in the face of uncertainties.
Consider a robotic arm tasked with precision assembly in a dynamic environment. Here, the predictive capabilities of MPC come into play, allowing the system to anticipate changes in load, adjust trajectories, and optimise control inputs in real time. The result is a level of accuracy and responsiveness that surpasses what traditional PID controllers can achieve.
In an aerospace application, where external forces on an aircraft may vary dramatically during flight, adaptive control strategies become invaluable. The system can continuously adapt its control parameters to maintain stable flight, compensating for changing aerodynamic conditions and ensuring the aircraft’s safety and performance.
In summary, the introduction of advanced control algorithms like MPC and adaptive strategies revolutionises motion control. Their predictive and adaptive capabilities outperform traditional PID controllers in scenarios demanding precise and adaptive control. Through comparative analysis, we witness their transformative impact in industries ranging from robotics to aerospace.
Conclusion
In conclusion, the synergy between TwinCAT, CODESYS, IPCs, motion sensors, high-level vision systems, and advanced control algorithms collectively drive innovation, efficiency, and precision in a wide array of industries, especially manufacturing. For those looking to integrate CODESYS into their automation systems, it involves a seamless process of installing the CODESYS development environment and configuring it to work with compatible PLC hardware. This allows for a smooth transition and integration of CODESYS alongside existing systems. For more detailed guidance and expert consultation on incorporating CODESYS into your automation setup, feel free to contact our team.
Contact us HERE if you’re interested in implementing CODESYS in your industrial projects to unlock its benefits and drive innovation in your industry.
Or to learn more about what we can do to help your automation requirements, please click projects, products & services.
Ti2 is currently very focused on working with its global partners to secure stock and avoid long delay times in delivering products to their customers. Together with our trusted partners, we are here to provide solutions for your needs.
Please click here to email us your inquiry, we would like to hear from you.