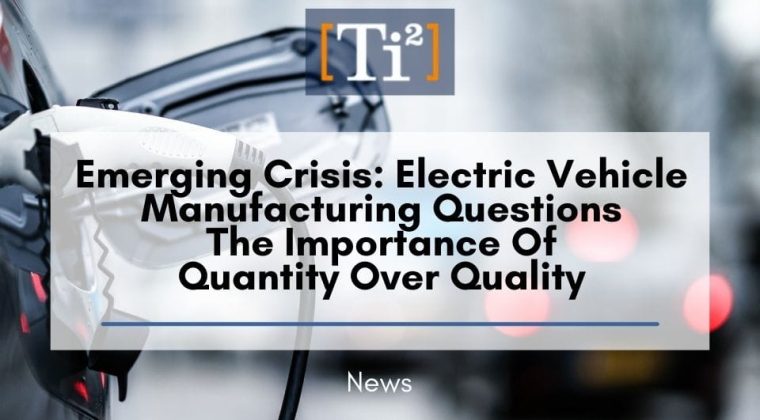
Splashed over countless printed and digital media is the insane growth that can be evidently seen in the market demand for electric vehicles. Indirectly, this has surfaced a number of challenges that EV manufacturing companies need to face as the medium tier of the supply chain.
Below is a statistic based on research done on European Transport. The EU transport research explored the characteristics and trends of electric vehicle crash in Norway and the result is quite alarming.
According to the case study: The EV crash count was zero in 2011, but reached 112 in 2018, occupying 3.11% of today crashes. Totally, 35,441 ICEV crashes and 342 EV crashes occurred in the survey period.
EV manufacturing is indeed at its peak performance with explosive market demand for not only quality but moreover, quantity. The challenge, however, is with increased quantity priority, manufacturing quality declines to a point where safety is compromised.
The ideal trifecta of a capable EV product is high-performing, cost-competitive, and consistent. Now, although the safety of the passenger may have been not been caused by the machine itself, there are high chances where machine failure is a variable.
Manufacturing indeed has a comprehensive batches of multi-step process that are not very cost-efficient when quality is main priority. In batch processes, engineers have to consider the ram up and down of different processes, and putting undue stress on the reactor and equipments. This can lead to failures and poor product quality.
To increase revenue profitability, reduce time, and implement short-term simplicity, there must be a clear underway of earl batches process but engineered into a single step continuously afterward to increase and maintain quality.
EV is highly different than other transportation and technologies with internal combustion engineers. This requires new safety hazards, which mainly relates to the high-power equipment characteristics.
The presence of high voltages and battery chemicals are new risks that should not be overlooked.
Several safety aspects to consider in EV safety are:
- Electric system
- Battery charging
- Vehicle maintenance, operation
- Man-training
- Functional system
Several international EV strandardisation committees are:
- IEC TC 69
- CENELEC TC 69X
- ISO TC22 / SC21
- CEN TC 301
Typical voltage levels on EV are:
- 48-120 V for cars and small vans
- 96-240 V for large vans and sometimes for small vehicles.
- 300-600 V for buses
For AC drives, higher voltages are used. In a typical EV environment, the characteristics are low skin resistance (BB2) and conductive bodies contact (BC3). Higher voltages used are 200V on small vehicles and the security extra low voltage level is 25 V AC or 60 V DC. Safety hazards are crucially important for voltages used on EV to prevent electrocution through direct/indirect contact.
To protect against direct contact, a key or tool must be in place to protect the live electrical equipments through the opening of doors, lids, and bonnets. The conventional protection degree, commonly, is IPXXB or IPXXD.
Indirect contact are usually correlated to frame faults – usually entailing spurious connection between the traction circuit and the vehicle frame. Frame faults may lead to :
- Short circuits
- Electrocution
- Uncontrolled operation
To prevent, make sure to;
- Build a fuse within the battery pack, best in the electrical centre of the battery
- Isolate the vehicle frame from traction circuit and make sure it does not form any part of the power electrical circuit
- Connect all conductive parts of the vehicle, specifically accessible parts or those that are adjacent to the electrical equipmenets to an equipotential connection.
- Ensure routine maintenance for frame fault leakage detection and monitor permanent frame fault.
- Present a system activation warning device in all EV, when it is silent or not moving to prevent unintential actuating of traction circuit.
There are many more safety hazards, maintenance, and prevention that requires strong organising and quality check. Thus the exact reason why the manufacturing of EV, as much as it is important to keep the quantity aspect of the manufacturing, is also very necessary to keep all processes of QC (quality control) in place.
Those that are short-sighted have no benefit. Instead costly, and inefficiently, ultimately losing the trust of the customers.
Instead of reducing processes, consider investing in high-quality, intelligent, and robust software options and machines that will help large-scale productions.
Ti2 Automation offers automation products with expertise from world-class suppliers. We provide robus competitive industrial automation solutions helping EV manufacturing companies among other emerging industries.
To learn more about what we do and how we can help your interoperability requirements, please click projects, products & services.
Ti2 is currently very focused on working with its global partners to secure stock and avoid long delay times in delivering products to their customers. Together with our trusted partners, we are here to provide solutions.
Please click here to email us your inquiry, we would like to hear from you.
Article inspired by ETEC, Forbes, Rockwell, SME, Elsevier, and Ti2.