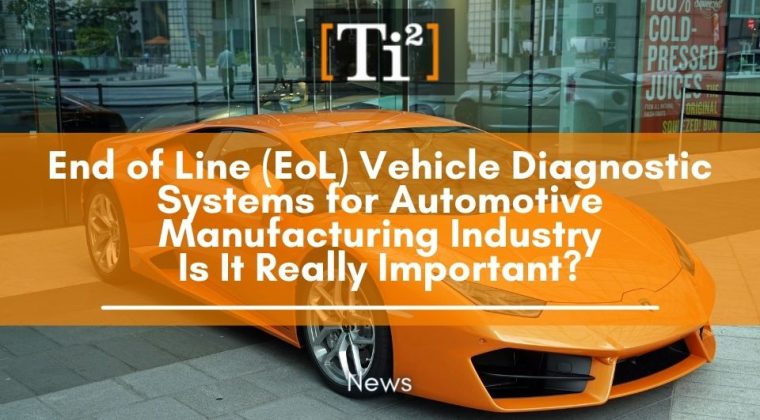
EoL (End of Line) vehicle diagnostic system is a great pioneer in the automotive manufacturing industry where improving efficiency, quality, and safety standards became constant goals. The automotive manufacturing industry stays competitive with over 79 million motor vehicles produced around the world in 2021, this is a 1.3% increase from 2020. In addition, around 6.75 million units of electric vehicles are produced with a significant rise according to the Electric Vehicle World Sales Database.
Innovations and upgrades are always in the making, one of them includes the EoL diagnostic system. With this system, all types of vehicles can be diagnosed from cars, trucks, buses, etc. This essential part of the manufacturing process facilitates end-of-line testing, a standard procedure in the automotive industry. The testing must be conducted before the product is shipped out of the plant and checked for quality control. Any failures, defects, malfunctions, or errors but be thoroughly filtered to fulfill safety standards. In addition, this is also a very important stage in the supply chain where a company’s reputation and the brand standard are at stake.
One of the main testing measurements is the NVH level. NVH stands for Noise, Vibration, and Harshness. It measures the tactile and aural ability of the vehicle to keep NVH exposure to a minimum. If a manufacturing plant fails to conduct proper QC, the cost of vehicle callbacks may cause higher losses. Recalls due to rework, scrap, and product failures can also damage a business’s reputation in addition to revenue declination. This represents the company’s inefficiencies, incapability to test and diagnose, and moreover, will cause lower confidence for shareholders to trust and support the company.
Today, manufacturing must be price, on-time, competitive, cost-efficient, and quality-assured. A way to improve the manufacturing process and wrap up reliably is with an End-of-Line vehicle diagnostic system.
What is EoL?
End of Line testing is meant to test the functionality of the manufactured product. It allows a profitable assembly with a low rate of failures and final reliable products. When testing, it’s important to consider real-life factors and the environment all products will encounter once it’s out of the manufacturing plant. Harsh road conditions, weather, user mindset, as well as other variables must be put into consideration to make sure that measuring responses are simulated to relevant conditions. During testing, the throughput rate (flow rate) must also be tested to calculate whether it is tangible.
Benefits of EoL Vehicle Diagnostic Systems
- Visibility and prevention – Reduces the failure rate of an assembly line
- Brand reputation – Improves the company’s image by providing a safe and reliable final product.
- Cost efficient – with fewer failures there will be fewer recalls and warranty claims.
- System efficiency – Optimises the assembly line and the overall production process.
- Speed and agility – EOL can help you quickly identify vehicle defects and ensure your products leave the workshop in pristine condition.
EoL Challenges
End-of-Line testing is not a cheap solution, the cost is relatively high in the market. Additional equipment and energy consumption can lead to spending more resources on the test. However, the key to this investment is to properly ensure that the manufactured products are as promised to the market. Consider the circumstances where testing is not conducted and the losses may cause severe company damage or even bankruptcy due to various reasons. It may be a legal lawsuit from an unkept product promise, perhaps even safety hazards that may cause harm to the consumer. Everything and anything is possible. Investing in a smart EoL diagnostic system is the smart move to make.
Usual EoL identifies malfunctions, errors, or problems at the end of the manufacturing process. This may be inefficient as fixing may still cost casualties.
- Testing system developed with 4Control, an IEC61131-3 product;
- Vehicle ECU communications using Softing DTS7 & EDICusb;
- Interprocess communications utilising OPC.
Conclusion
The automotive industry is an everlasting industry. Manufacturers and investors are in the momentum to provide the perfect automotive solution to the market. With the same goal of achieving innovations while meeting safety standards, regulations, and customer demands, End-of-Line testing will provide solutions to various problems, allowing manufacturers to work more in their business, than on their business. Assure safety and reliability with EoL’s complete diagnostic system and achieve a bigger revenue goal for the coming winning years.
To learn more about what we do and how we can help your interoperability requirements, please click projects, products & services.
Ti2 is currently very focused on working with its global partners to secure stock and avoid long delay times in delivering products to their customers. Together with our trusted partners, we are here to provide solutions.
Please click here to email us your inquiry, we would like to hear from you.
Article inspired by acerta, goepel, siemens, Acea, and EV.