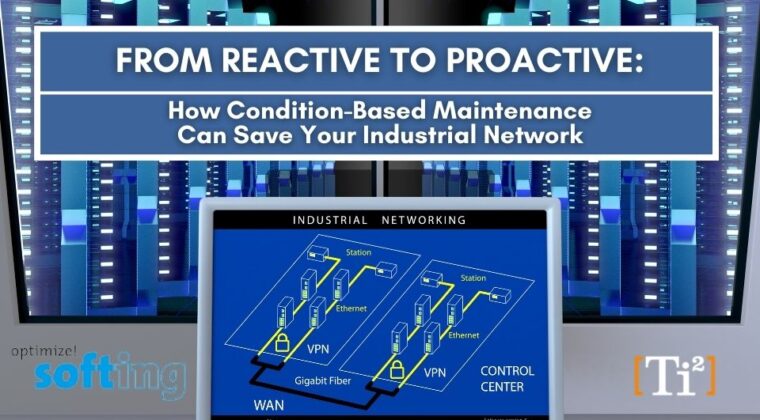
The value of your machinery and equipment is tied to its reliability, and when machines are down, it’s hard to keep up with demand. However, as technology advances, plant operations are provided with smarter solutions to operate at a constant level without breakdowns with advanced abilities to forecast and better maintaining equipment and machinery avoiding delays and large cost implications.
This article will discuss the benefits of condition-based maintenance (CBM) for industrial networks, as well as the standard techniques and tools used to implement CBM. It will also talk about how to implement CBM in your own industrial network, including real-world examples of CBM in action.
With condition-based maintenance (CBM), your network can predict when and how the equipment will fail, allowing you to plan ahead and avoid downtime. CBM uses data from all aspects of your machine, including temperature sensors, vibration monitors, actuators, alarms, and other data analytics or diagnostic tools to find the root cause of issues before they become too severe.
CBM can be applied across any industry with industrial products or machines, including manufacturing plants and oil refineries. It’s also cost-effective: a recent study found that CBM can save organisations up to $2 million per year in avoided costs. It is easy to implement: companies have implemented CBM for as little as $100K per year on average—and have seen immediate returns on their investment within 12 months.
Reactive vs. Proactive Maintenance
When it comes to industrial networks, reactive maintenance is typically the gold standard. It’s been used for decades, and it’s well-documented in the literature. But there’s a new trend on the horizon: proactive maintenance, or condition-based maintenance (CBM).
Reactive maintenance is a manual process of checking equipment, finding issues, and fixing problems as they arise. This approach can be expensive and time-consuming since problems don’t always present themselves when it’s convenient to the operator.
Proactive maintenance is a practice that focuses on identifying and addressing problems before they occur—instead of waiting for a problem to happen and then fixing it after the fact.
Condition-based maintenance (CBM) is a strategy for maintaining production equipment that considers all interdependent factors leading to failure – which we categorise as proactive maintenance.
This type of approach has benefits for both industrial networks and their users because it prevents issues from arising in the first place and saves money by reducing downtime and having to replace components early on. It also helps companies meet higher quality standards while reducing environmental impact through decreased waste generation during production processes (e.g., less time spent cleaning up spills).
The Benefits of CBM for Industrial Networks
Condition-based maintenance isn’t just some buzzword; it’s based on sound science and best practices that have been developed over many years by industry experts at places like Ti2 Pty Ltd and together with Softing Industrial. By implementing CBM in your industrial network system, you can take advantage of these benefits:
- CBM helps reduce costs by preventing large-scale failures that can take down an entire plant—or even put an entire company out of business.
- CBM can save time, money, and downtime by identifying problems before they cause damage or downtime at your facility.
- CBM increases equipment efficiency, ultimately increasing plant quality and quantity through schedule-based maintenance based on actual operating conditions rather than projected costs or predictions.
CBM’s method of monitoring and managing industrial equipment uses data from the equipment itself to predict when maintenance is needed. This method is also commonly adopted by industries such as oil and gas, mining, agriculture, and manufacturing aside from aviation and the automotive industry.
CBM was actually developed by NASA in the 1960s as part of their mission to send humans to space. The project was called VULCAN (Vehicle Undergoing Long Term Care Analysis Network), and it monitored the health of space shuttle parts with sensors that could tell when a part was about to fail.
In recent years, CBM has been applied more widely in industry, both in military and civilian contexts. In the military context, CBM helps ensure that missiles are always ready to fire; in civilian contexts, it can help companies reduce costs by reducing downtime and increasing uptime.
This explains how important and critical using CBM is for many industries.
A growing number of case studies in different industries demonstrate how CBM systems have worked successfully in practices such as CBM Systems for Aviation: Fighter Aircraft Engines and Commercial Aircraft Engine Components.
CBMs are often implemented in conjunction with Industrial Internet of Things (IIoT) systems, but they can be applied to any industrial network that uses sensors to monitor equipment conditions.
With machine learning, when equipment is likely to fail based on data collected from sensors as mentioned above, the CBM systems can automatically schedule the maintenance actions or even take action themselves, such as shutting down an engine or opening a valve.
A CBM system can be implemented with little or no change to existing instruments and processes, which makes it a useful complement to other approaches like predictive maintenance or condition monitoring.
Common CBM Techniques
There are many common CBM techniques: machine learning, Bayesian inference, artificial neural networks, and expert systems are just some examples. These techniques are not mutually exclusive—Together with Softing Industrial, Ti2 uses multiple techniques together in order to achieve the best results for particular situations. CBM was actually developed by NASA in the 1960s as part of their mission to send humans to space. The project was called VULCAN (Vehicle Undergoing Long Term Care Analysis Network), and it monitored the health of space shuttle parts with sensors that could tell when a part was about to fail.
In recent years, CBM has been applied more widely in industry, both in military and civilian contexts. In the military context, CBM helps ensure that missiles are always ready to fire; in civilian contexts, it can help companies reduce costs by reducing downtime and increasing uptime.
This explains how important and critical using CBM is for many industries.
A growing number of case studies in different industries demonstrate how CBM systems have worked successfully in practices such as CBM Systems for Aviation: Fighter Aircraft Engines and Commercial Aircraft Engine Components.
There are many tools available for performing CBM today including manual inspection, data analysis software, and/or Artificial intelligence algorithms.
Remote monitoring uses sensors to monitor the condition of equipment from afar while CBM maintenance algorithms use historical data about the performance of an asset to make predictions about its future performance.
Lastly, predictive maintenance systems use machine learning algorithms to make predictions about when an asset will fail, so that preventative maintenance can be performed before catastrophic failure occurs.
Contact us HERE to learn more about our case studies.
OR view the TH SCOPE software product to learn more about Softing Industrial’s comprehensive network diagnostics tool that enables permanent network monitoring & management.
work
TH SCOPE is a software product for industrial network diagnostics and network management. Geared to plant operators and maintenance personnel, TH SCOPE is an all-in-one, easy-to-use solution for permanent monitoring and predictive maintenance, for acceptance testing and for troubleshooting. Combined with TH LINK components, the product supports PROFIBUS, PROFINET, EtherNet/IP and Modbus TCP protocols.
To learn more about what we do in partnership with Softing Industrial in regards to engineering, runtime, visualisation, motion CNC robotics, Fieldbus, safety, and how we can help your industrial network requirements, please click projects, products & services.
Ti2 is currently very focused on working with its global partners to secure stock and avoid long delay times in delivering products to their customers. Together with our trusted partners, we are here to provide solutions for your needs.
Please click here to email us your inquiry, we would like to hear from you.