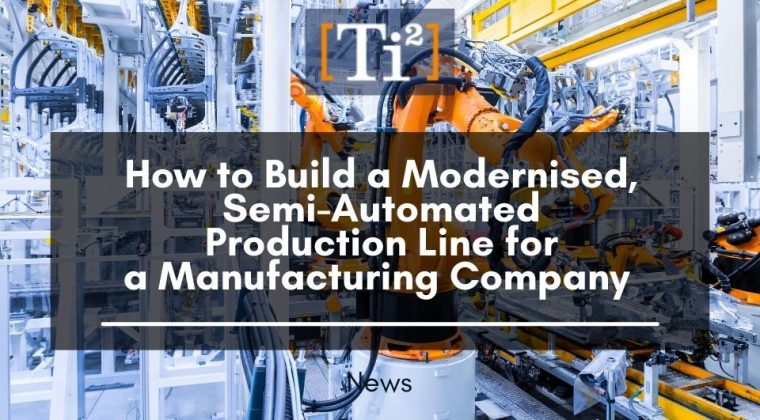
In a fast-paced global manufacturing marketplace, time is of the essence. To this end, manufacturers are increasingly adopting automation in their production processes to streamline their workflow and cut costs. However, most automated manufacturing plants are still very much a human-led operation. This article explores how a semi-automated production line can streamline your manufacturing process while keeping human workers front and centre.
Ti2 have completed a modernised, semi-automated production line for an Australian company producing Sleep Apnea products. This project included assembly stations, product flow control, product scheduling, and raw materials management.
Supplied with only a one page requirements document and an extremely short time line, Ti2 designed, built, installed, and commissioning a complete semi-automated production line, which included the ability to run multiple sized products, and manage the raw materials delivery and quality control.
What is a semi-automated production line?
A semi-automated production line is a manufacturing process that combines the hand-made techniques of craftsmanship with the productivity of automation. As such, the line is semi-automated, maintaining the human-led manual elements while adding in the mechanised, automated processes that are key to running a fully automated production line. With a semi-automated production line, you’ll still have plenty of human workers on the line but they’ll be supported by certain automated processes that will speed up their workflow and boost overall production.
A study by McKinsey & Company found that “87% of the hours spent on activities performed by workers in production occupations are automatable — the most of any manufacturing occupation.”
According to Fronetics, it doesn’t stop there. “Even among other occupations in manufacturing (for example, engineering, maintenance, materials movement, management, and administration), however, there is still significant opportunity, with approximately 45 percent of these working hours automatable as well.”
How does a semi-automated production line work?
A semi-automated production line is a hybrid of manual and automated processes, balancing the best of both worlds to create a streamlined operation. On the one hand, you’ll have your manual processes that require the expertise and dexterity of human workers.
On the other, you’ll have your automated processes that require the precision of robotics. With a semi-automated production line, you’ll have a variety of automated processes mixed in with your manual operations.
These automated processes can be broken down into three categories:
- Precision material handling – For example, a fully automated palletising system that stacks finished products onto pallets for transportation.
- Robotic production – For example, a pick-and-place robot that places raw materials onto the production line or an assembly robot that completes the final assembly of a product.
- Cyclical production – For example, a conveyor belt system that transports products through the production line or a robotic dispensing system that dispenses chemicals at certain points along the production line.
According to the McKinsey study, companies are suggested to consider the following four factors when making decisions about what to automate:
- Technical feasibility
- Cost associated with developing and deploying necessary hardware and software
- Cost of labor and resultant “supply-and-demand dynamics”
- Benefits beyond labor substitution, such as increased output and quality, and fewer errors
What does a modernised, semi-automated production line look like?
The production line a manufacturing company build will depend entirely on the type of product manufactured. However, there are some basic features that will make the production line work smoothly and efficiently.
- Raw materials – To start with, a good feedstock capacity is required. This includes any chemicals or variables needed in the production process as well as the products that will be created.
- Product feeders – These are used to feed raw materials into the production line as needed. This can include feeders for things like sheets of paper or rolls of fabric.
- Product finishing – At the end of the production line, include product finishing equipment such as cutters, sealers, or shrink wrap machines.
Three steps for building a semi-automated production line
When building a semi-automated production line, it’s important to plan your production process from start to finish. This will help you identify areas of your production line that can benefit from automation, highlighting bottlenecks and inefficiencies that need addressing. For example, you might notice that you have to manually shuttle products between workstations, putting a strain on workers and slowing down the production process.
To resolve this, you could add in a shuttle conveyor to shuttle the products from one station to the next. Put simply, the first step to building a semi-automated production line is to map out your production process.
- What products are you making?
- What raw materials are required?
- Where can you improve?
With these questions answered, you can start to add automation to your production line to help it run more efficiently.
Conclusion
A semi-automated production line is a middle ground between a fully manual production process and a fully automated production process. It’s an efficient production model that can be scaled to grow with the business. As the name suggests, the best semi-automated manufacturing facilities are a hybrid of automated and manual operations. They also have a clear and streamlined workflow, with all parties working together efficiently and effectively. Moreover, if you have a computerised production line, you can even produce computer-generated designs for your facility or plants. This ensures end-product and quality assurance.
To learn more about what we do and how we can help your automation requirements, please click projects, products & services.
Ti2 is currently very focused on working with its global partners to secure stock and avoid long delay times in delivering products to their customers. Together with our trusted partners, we are here to provide solutions.
Please click here to email us your inquiry, we would like to hear from you.
Article inspired by Fronetics, McKinsey & Company, and Ti2.