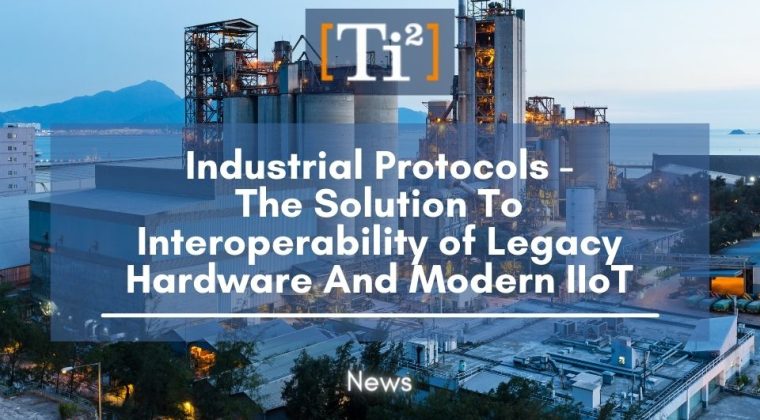
Many industry leaders we’ve met have shared the same concerns. The interoperability of industrial network protocols. It has changed, and as some of us say that it’s new, but the definition of ‘new’ is very relative when most protocols have actually been available for over 10 years.
As seen in the illustration sourced from Johnathan Hottel’s discussion material of efficient IIoT communications, many protocols can be used in similar scenarios with similar functions, however, protocol use overlap doesn’t mean that all is a good fit, and may depend on the conditions.
When considering the expectation vs reality aspect, the results are much more complex than we think. For instance, testing using a 100/1000 network vs on a slow SCADA network.
It’s important to make sure that the testing process is not biassed towards a certain protocol.
Another struggle may be the constraint of budget. With limited resources, major upgrades may require a longer time to implement, and the best you can do as manufacturers would be to work with what you have and utilise it to its optimum potential.
With industrial network protocols as the basis of communication between legacy hardware and new IoT technology, several strategies can be used to separate legacy and new.
As the father of Greek didactic poetry, Hesiod, said, “Preserve the mean; the opportune moment is best in all things.”
All industry-specific network protocols are designed and built with specific purposes, for specific environments, with their own strengths. Now with the emergence of IIoT, wireless and Ethernet open up new possibilities for connectivity. This is a great improvement to help integrations as interconnecting protocols is essential to make sure trusted legacy hardware communicates like a modern IoT device.
The idea is to preserve the good hardware and offer old machines/devices a new layer for IoT integration. This will help focus on the practical benefits and not just the upgrades.
Secured Modbus can be a starting point, with a newly added layer of MQTT, TLS security, and Sparkplug B for a unified industrial solution.
Ultimately, a good strategy is to offer an additional layer that will normalise data from the edge and transfer it to a centralised common protocol. A centralised gateway will then be accessible by any cloud and software platforms for more necessary applications.
HART and Modbus have also been made easy by Softing’s commKit for industrial plants.
Josef Luttenbacher, Product Manager at Softing Industrial says: “Industrie 4.0 and derived concepts such as the NAMUR Open Architecture (NOA) are focusing on the extensive data that digital field devices can supply for diagnostics and asset management. Consequently, we see a growing demand from device manufacturers to replace the analog current loop interface and HART modem with a digital Fieldbus interface for FOUNDATION Fieldbus or PROFIBUS PA. This usually requires extensive and costly development work for both software and hardware. For those, who do not have the capacity for large-scale investment, our commKit offers an inexpensive retrofit and guarantees a fast time to market.”
Industrial Network Protocols
Fundamentally, there are four layers in a typical industrial network setting.
1. Field Layer – This layer includes sensors, transducers, and actuator nodes. The objective is to collect environmental or process control data. Information is then relayed to the controller for monitoring.
2. Control Layer – PLCs and DCS provide local control to specific domain groups in the plant through digital or analog modules. They execute and process instructions: logic, sequencing, timing, counting, and arithmetic to control.
3. Supervisory Layer – With SCADA system, the plant control systems interoperate with human-machine interfaces to drive plant operations. Reports and continuous remote monitoring provide alerts and views of the entire managed system. Key functions: data processing, logging, and historical trending.
4. Execution and Planning Layer – mainly covers:
- Manufacturing and engineering execution by MES (Manufacturing Execution Systems)
- Resource and equipment scheduling with ERP (Enterprise Resource Planning) system
- Work in Progress job specifications
Although both wired and wireless networks each have their own protocol sets, most wired are standardised by Fieldbus or Industrial Ethernet, at which wireless include Wi-Fi, Cellular, Bluetooth, and ZigBee are all being used to varying degrees. Today, IO-Link is also gaining popularity.
Many industry leaders are focusing on increasing Omni-interoperability beyond the technical realm. The goal is to have a seamless transfer of knowledge between actors in a system where humans, machines, organisations, and entities are all on the same level. This will be a new value that integrates the public and private cloud, operational system, and business domain. A new opportunity for protocol harmonisation in the industrial environments.
Among some of the factors influencing the evolution of industrial communication protocols, interoperability, real-time/determinism, mobility, operating environment, scalability, and power consumption plays the biggest role.
Some difficulties may include the incompatibility among heterogeneous devices at various levels, as well interoperability from plant floor or ERP layers. This requires common platforms like OPC US to allow common communication language.
Ti2’s reliable partner, Softing, now offers OPC UA C++ SDK that has been extensively updated to support Reverse Connect and access to a Global Discovery Server.
With the new version 5.70, Softing has enhanced the functionalities and ease of use of its OPC UA C++ Software Development Kit (SDK). With the help of Reverse Connect, users can now easily establish a secure OPC UA connection with OPC UA clients across the firewall using their product’s OPC UA server without opening internal binding ports. Use cases for Reverse Connect include company-wide, cross-domain connectivity, Industrial IoT and Industry 4.0 applications, and secure field-to-cloud OPC UA data connections.
In addition, the OPC UA C++ SDK now allows access to a Global Discovery Server (GDS). Two models are supported: “Push” – where the request for a particular transaction is initiated by the server – and “Pull” – where the request to transfer information originates from the client. The OPC UA GDS concept allows the configuration of a network-wide detection of OPC UA servers. Furthermore, it offers the functionality for central management of the certificates used in OPC UA.
In specific usage, time-sensitive messages are crucial, the good news is that communication standards and protocols like TSN and Profinet IRT have improved. Ti2 partners with Sichuan Odot Automation Systems for a range of reliable and robust modules and communication options at very competitive prices.
As for the operating environment, a safe plant floor is important with stable connectivity channels. For manufacturing, PROFIBUS PA has dominated the industry with a recently added physical layer on Ethernet (Ethernet-APL).
In conclusion, the separation between ‘legacy’ and ‘new’ is now highly possible with Omni-interoperability. With the right communication protocols, seamless connectivity among devices is very possible without major disruptions.
To learn more about what we do and how we can help your interoperability requirements, please click projects, products & services.
Ti2 is currently very focused on working with its global partners to secure stock and avoid long delay times in delivering products to their customers. Together with our trusted partners, we are here to provide solutions.
Please click here to email us your inquiry, we would like to hear from you.
Article inspired by arrow, utthunga, Softing, HART, Hottel, and Ti2.