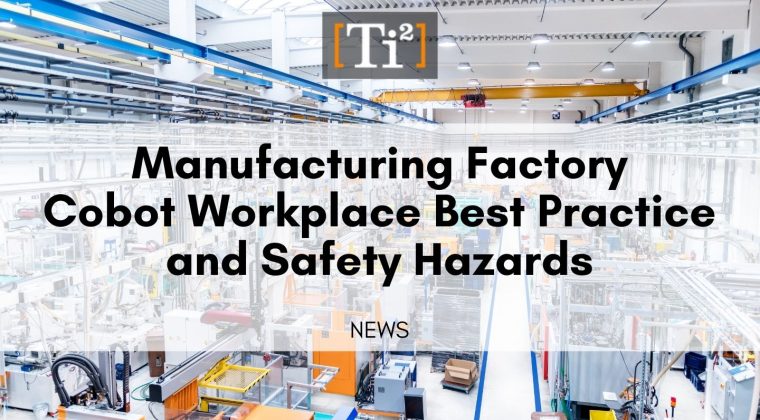
Manufacturing with cobot workplace safety hazards isn’t a game, but you definitely need a game plan for it. In order for everyone in your team to understand the importance of workplace safety, they must understand the reason behind it and how history played a part in it.
There are plenty of variables and factors that need to be considered, especially where humans and robots co-exist. Where digitalization and the industrial revolution are involved, following a safe and standard operating procedure is the way to go to produce not only the best quality of service and product but also maintain the best workplace and workforce environment.
Aging back to decades ago, robots operate in a constricted parameter. Why? This was considered a safety measure. Robots were in no way meant to play a facilitating role.
The first cobot or so-called collaborative robot was invented in 1996 by J. Edward Colgate and Michael Peshkin. A cobot is designed to have the capability of learning multiple tasks to facilitate human beings. This is the total contrary of traditional, autonomous robots that are designed to do one thing at a time, independently, and stationary.
Working closely with cobot(s) lacks distance and physical separation. In order to prevent fatal accidents, cobots are often complemented with sensory technologies to enable cobot safety requirements.
A cobot is usually identified as ‘safe’, only if it doesn’t have any ability but to move around. Force-limited, rounded edges and covered non-pinching joints are some basic criteria to keep humans safe during collaborative operations.
Workplace Best Practice
Workplace safety responsibility lies with the end user, who purchases, installs and applies these smart applications into their operations. Hence, ISO (International Standardisation) released important guidelines – on how to better regulate on how manufacturers ensure the safety of their workers besides the standardised emergency stop buttons, safety light curtains, screens, gates and speed limits for example but now and for the future, as operators work more with technically advanced machinery. Comprehensive checks need to be done and subject to the cobot’s task will determine the level of safety implications necessary. Then, as and when any robotics are reprogramming, thorough re-checks will be required and safety procedures will need to be updated accordingly.
Some rules for cobot/robot safety may include but are not limited to the followings:
- Conduct a comprehensive risk assessment to see if the workplace environment is feasible for both cobots and humans.
- Test out built-in safety measures & emergency stop switches.
- Define both cobot and operator safety assurance such as:
- Dynamic collision avoidance
- Trajectory planning algorithms
- Functional planning algorithms
- Functional gradient techniques
- Agile maneuverable joint angles
- Computational work-cell design
- Sensory work-cell safety zoning
- Dynamic motion limiting devices
- Robotic perception: depth camera
- Ensure all safety equipment are available and worn within the collaborative environment.
Manufacturing Factory and Safety Hazards
Where machines and humans are always on the move, manufacturing factories can be dangerous. Human beings are still the priority and falling, tripping, slipping, or even hitting on certain things can cause injuries or even death. There’s a saying – “Safety Rules Are Your Best Tools.”
This is why safety breaches are considered crimes and are internationally set out to provide the best protection to all workforce.
Workplace injuries in the Manufacturing and Industrial Industry – “Australian workers in the manufacturing and industrial industry account for 20% of all serious workers – compensation claims which translates to 73 workers per day suffering a workplace injury in this industry”. Source: Walker Law Group.
According to SafeworkAustralia (ADD), in the five years from 2008–9 to 2012–13, there were 107 manufacturing workers killed. The most common causes of fatalities were vehicle incidents, being hit by moving or falling objects, falls from heights and being trapped by moving machinery. 87,285 serious injuries reported, The most common types of injury were joint/ligament, muscle/tendon, wounds, lacerations, amputations, internal organ damage, and fractures.
Besides common vocational hazards, electrical hazards have put plenty of people at risk. Electrocution may come from loose machinery parts, unfastened electrical panels, exposed wiring, or even improperly installed modules. Make sure installation and insulation are done properly across all components.
Lastly, with various types and pieces of machinery, a blueprint and systemic infrastructure must be ensured so no accidental startup or energy discharge occurs. Apply all necessary precautions and signage for warnings, lockout safeguards, and employee warnings in the right spots.
Ti2 is currently very focused on working with its global partners to secure stock and avoid long delay times in delivering products to their customers. Together with our trusted partners, we are here to provide solutions.
To learn more about what we do, please click projects, products & services.
Please click here to email us your inquiry, we would like to hear from you.
Article inspired by Southwest Research Institute, APAC, Automate, NIOSH and DTI.