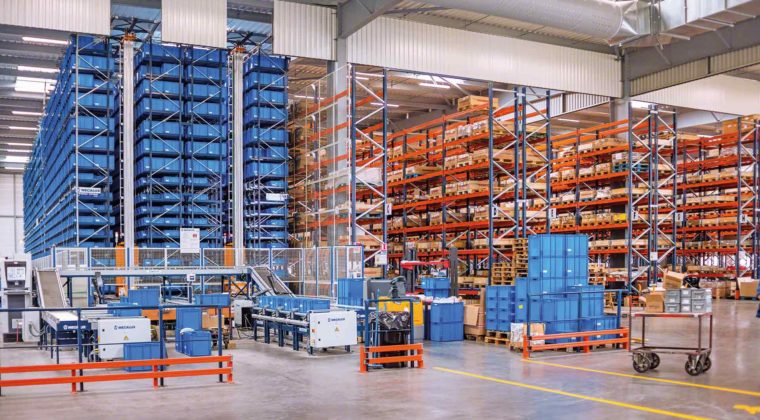
With the growing evolution of the technologies the automated storage and retrieval system (ASRS) market is also growing in the pas decade with an 8% growth annual average. Food and beverage, retail, and automotive are the industries that have experienced a fast rate using ASRS. The growth of e-Commerce will be a major factor which will drive the development of the ASRS market together with the automated platform.
Replacing traditional storage and product handling operation using forklift, and installing ASRS is the most effectual investment a manufacturing or warehousing facility could make, it increases throughput, accuracy, and safety which also reduces product damage and human error. But if integrated ASRS is used into a highly customized operation could be disadvantageous. A careful financial analysis must be conducted by the companies who seeks to invest in this technology considering the high initial costs.
The pros of using an Automated Storage and Retrieval System (ASRS)
High-Density Storage
Space limitations is the enemy of all manufacturing and warehousing facilities. With the increase of production and expand the storage capacity which are design and built in a certain considerations needs to exceed it’s existing capacity. Most companies are only able to add a square footage horizontally to the building through construction which is costly and sometimes impossible.
Increasing the storage without adding square footage to the building is the ASRS job, it’s volume efficiency or ratio of storage capacity is on the highest level compare to the square footage which makes ASRS as the commonly referred to as high-density warehouse.
Better Safety of Operations
Eliminating the risk which is associated in using forklift and also forklift operations can be done when using ASRS. Using ASRS to intervene when needed can be done using a graphic user interface (GUI) or human-machine interface (HMI). Requiring ASRS to have safety interlocks, lockout/tagout (LOTO), and other procedures to be followed should be able reduce the risk and is much more safer option than using forklifts when it is required to enter the are of the moving equipment if a maintenance is needed or if there is a major failure that needs to be attend.
Increased Accuracy and Efficiency
With ASRS handling the products with it’s programmed to execute repetitive task with high precision could reduce the damages which are usually caused by human error when handling the product using forklift or other means.
ASRS are all controlled by a warehouse control system (WCS) or warehouse management system (WMS) which would enable ASRS to transfer product tracking data automatically. The usual manual operation is prone to many inaccuracies with it’s strict process sequence that needs to be followed. With WCS or WMS of ASRS these problem could solve and eliminated.
The Cons of an Automated Storage and Retrieval System (ASRS)
Initial Investment
ASRS is a large and complex construction that needs special materials and reinforcements for the structure to withstand the loads that is to be stored which makes it inaccessible to some business. But in today technology there are now ASRS that could be build that would suite a smaller space and less industrial setting. Manufacturers and warehouse facilities are now not the only ones that are using ASRS, supermarket chains, pharmacies, and distribution center are also beginning to explore this technologies for e-Commerce and online order fulfillment (micro-fulfillment).
Inflexible Tasks
ASRS are only built o perform a single type of task. ASRS storage location is varied in different sizes but it’s size dimensions cannot be adjusted. If adjustment to the already built ASRS would cost a lot which could cause a negative effect on the business when a new product would exceed the storage location. When building a ASRS it’s need a lot of consideration for the future projections of the production volume and production lines, which should be part of the equation when installing ASRS.
As with any automated system, ASRSs have advantages and disadvantages. Some advantages include increased storage density, safer operations, and increased accuracy and efficiency. On the other hand, some disadvantages are high initial investments and inflexible tasks. From a business perspective, high initial investments can be a large downside, but keeping a safe operation is a top goal.
Please contact us for further information