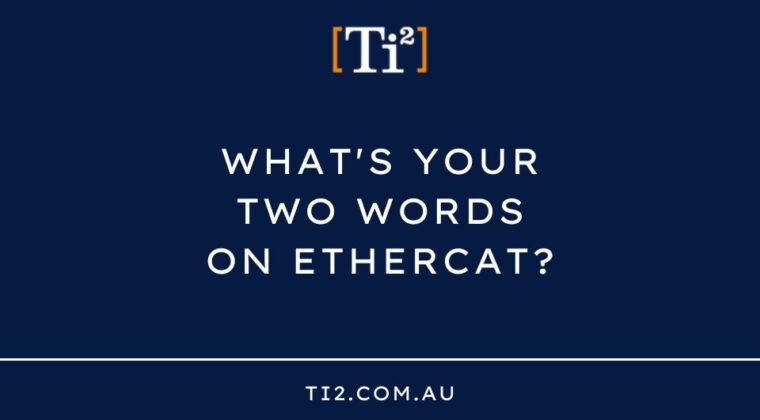
If there are two words to explain the purpose of EtherCAT for the industrial network, it’s speed and performance. A key challenge in industrial communications is real-time monitoring, and EtherCAT solves just that. Without real-time data monitoring, downtime and system error prevention is hard to manage and halt many communication capacities. In addition, the creation of EtherCAT as a high-performance industrial communication protocol has provided cost-cutting advantages to many companies.
EtherCAT is a powerful real-time Ethernet fieldbus system with an open protocol. With its short cycle times, low jitter values, and different network topologies, the system is standard in many industrial automation applications today.
In the past 4 days, EtherCAT Technology Group (ETG) has presented an informative series of EtherCAT events throughout Australia. It’s safe to say that EtherCAT has proven itself to be the ‘Big Cat’ in the automation industry.
In our past article, we shared a Quick Overview of EtherCAT and an introduction to EtherCAT’s Seminar Series Australia 2023.
EtherCAT’s roadmap for the future through gigabit performance and the integration of emerging communication technologies is focused on generating performance and accelerating competitive and advantageous applications.
This protocol has become a standard in the sector and its ability to meet real-time hardware and software requirements across various automation and applications are characterised as a real-time high-performance deterministic bus. According to a study on the industrial networks market, the number of new nodes connected to industrial networks increases every year, with a +10% in 2019 alone.
The EtherCAT protocol has a guaranteed cycle time of <=100 microseconds with a maximum jitter time of 1 microsecond. This standard allows a very predictable data transfer with precise timing and accurate synchronisation.
When the use of EtherCAT applications skyrocketed in industrial automation, it was clear for companies in the manufacturing and distribution sector that by choosing EtherCAT as their industrial Ethernet network, they would advantageously be winning over their competitors through cost-cutting cabling that is simple and cost-efficient. The best part? Not the low cost, but the opening towards devices of all houses and again, the real-time performance.
CODESYS EtherCAT master configurator works as one tool with an integrated infrastructure for PLC programming and Fieldbus configuration. The advantages of the seamless integration include:
⇒ Simple configuration
⇒ Fewer sources of error
⇒ Fast engineering
Read more about it here.
If you’re a system integrator or a user in the plant construction sector or the like, use controllers equipped with CODESYS EtherCAT support.
Millions of CODESYS-compatible single devices and over 1,000 different device types from more than 500 manufacturers offer you a large range of hardware for your automation projects. CODESYS Inside offers a selection of manufacturers that offer CODESYS-compatible devices. Alternatively, you can use the CODESYS Control SoftPLC Systems from the CODESYS Store. CODESYS EtherCAT is integrated into these systems and can be used immediately.
If you’re a manufacturer of programmable devices, implement the CODESYS EtherCAT support on your hardware. All you need for this implementation is the CODESYS Runtime Toolkit with EtherCAT support.
The EtherCAT master integration in the IEC 61131-3 development system CODESYS comprises:
- A portable protocol stack in form of a CODESYS library
- An integrated configurator for the master and the connected slaves
- A runtime system component for direct access to the Ethernet interface
- Diagnostics functionality in the Development System and the possibility to monitor the process through the IEC 61131-3 application
- Optional support of EtherCAT gateway modules to other fieldbus systems such as IO-Link, PROFIBUS, or the like
Other functionalities include:
- Distributed Clocks
- Different bus topologies
- Bus diagnostics: in the configurator and by the PLC application
- Network scan: Recognise and insert connected slaves
- EtherCAT redundancy: for systems with two physical Ethernet interfaces
- Supported layer 7 protocols: CoE (CANopen® / CAN application layer over EtherCAT) / SDO Communication, EoE (Ethernet over EtherCAT), SoE (Servodrive over EtherCAT), FSoE® (Safety over EtherCAT or FailSafe over EtherCAT), FoE (File over EtherCAT), VoE (Vendor over EtherCAT)
Functionality Configurator
- Semi-automatic configuration of the master or configuration in the expert mode
- Comprehensive configuration options
- Configuration of the slaves with EtherCAT XML files
- Flexible configuration of the process image and of the device-specific parameters
- Support of third-party EtherCAT stacks
- Export of EtherCAT XML files possible (ENI)
Supported Network Cards:
- Systems with Linux®: Via RAW sockets: all network cards
- Systems with Microsoft Windows and CODESYS Control Win: With PCAP interface (win cap): all network cards
- Systems with Windows and CODESYS Control RTE (Real-time SoftPLC):
- Realtek® 8139 (CmpRTL81x9Mpd) Realtek RTL8139 and compatible Ethernet-Controller, as well 8100/8110
- Realtek 8169 (CmpRTL8169Mpd) (Realtek 8169/810, RTL8111B / RTL8111D)
- Intel® EtherExpressPro1000 (CmpEt1000Drv) All gigabit adapters from Intel
- Intel EtherExpress PRO/100 (CmpEt100Drv) All 100 Mbit adapters from Intel
- Other system platforms: Adaptation of the runtime system component required
Ti2 Pty Ltd is the official distributor for CODESYS in Australia, offering automation products with expertise from world-class suppliers. We provide robust competitive industrial automation solutions helping manufacturing companies among other emerging industries.
To learn more about what we do and how we can help your interoperability requirements, please click projects, products & services.
Ti2 is currently very focused on working with its global partners to secure stock and avoid long delay times in delivering products to their customers. Together with our trusted partners, we are here to provide solutions.
Please click here to email us your inquiry, we would like to hear from you.