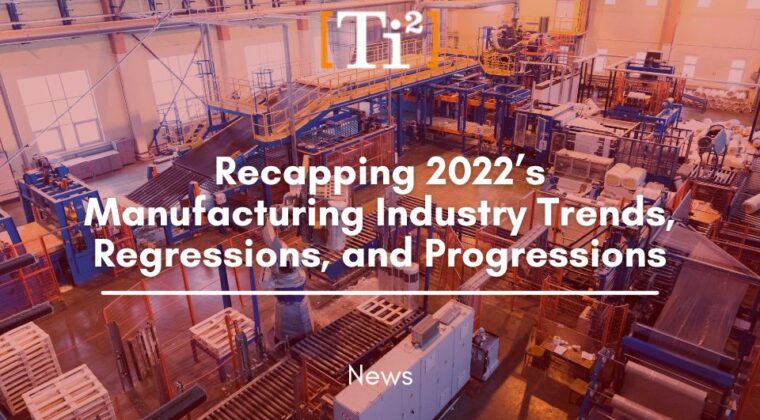
2022 was a year of survival. 2023 is a year of expansion. History will repeat itself and after every disruption, a surge of revolution and innovation is guaranteed.
Despite the short demise of manufacturing in 2022, the regressions have inspired progressions.
Essentially the seven factors that ensures expansion in the manufacturing industry includes:
- Labor/workforce
- Capital/financial resources
- Market demand
- Power supply
- Logistic/delivery
- Land/space
- Commodity
2022’s crises and regression includes:
- Higher demand
- Lack of labor or workforce and output
- Increased logistics or delivery rate
- Inflation – affects commodity price, logistics, and processing
- Trade restrictions – delays and compromised delivery security
- Factory closures
The overall facet may have improved compared to 2021 but was not any less challenging.
On the bright side, here are the trends and progressions that allowed COVID, and all other disruptions to act as a catalyst:
- Automation, smart technology, and digitisation
- Human resources/workforce standardisation
- Sustainable manufacturing (Circularity) and carbon neutrality
- Logistic and delivery – Offshore/onshore
- Market demand increase
Continue reading to see how each trend influenced progressions and how you should evaluate 2023’s manufacturing outlook for both the market and your manufacturing company.
Automation, Smart Technology, and Digitalisation
Smart factory adaptation through automation, smart software and technologies, as well as digitisation continue to proactively approach the manufacturing industry. With automation, smart design and digitisation, the followings can be achieved:
- Big data collection and analytics
- Predictive and accurate design and protyping
- Preventative downtime
- Effective and efficient maintenance
- Supply chain optimisation through process visibility and transparency
- Fast diagnostic system and process
- Increased market demand fulfillment
Prior to COVID, vendor lock-in was considered a stable option with specific brand and standardisation commitment. Post pandemic, a transition from vendor lock-in to LCNC (Low-Code No-Code) software, or a full-solution automation software provider that support various programming language for industrial automation is considered a cost-effective and time-efficient solution.
Due to different tasks at hand — repetitive, interlocks and/or concurrent processes and operations, different programming language is required.
Manufacturing industry today focuses on final user maintenance, efficient logistics, sufficient stock, universal standardisation and backward control reliability.
CODESYS is a leading hardware-neutral programming environment that purely concentrates on creating the most up-to-date programming and commission tools. CODESYS can be used to program over 1000 hardware controllers from over 400 different vendors.
CODESYS helps mid-tier automation companies with larger software teams to stay on top of automation developments and standards. With CODESYS, a team in-house is no longer required, and some top-tier suppliers have even used and rebranded CODESYS as their own tool.
End users employ CODESYS for successful creation of simple and sophisticated automation applications for industrial controllers that are used in factories, mobile machines, power and building automation systems, as well as many other areas.
Human Resources/Workforce
With no signs of slowing down, skills gaps, supply chain bottlenecks, and workforce shortages are still critical variables the industry have to overcome.
Automation is the most important solution that will significantly remedy workforce shortages. On top of that, ensuring quality and quantity output to fulfill market demand.
However, it is worth noting that more training and knowledge transfer will be required to ensure that a harmonious relation between the robots and the humans can achieve increased quality and quantity output with productivity, safety, and efficiency.
To do that, companies will require better vocational training and resources.
In 2023, the advancement of Industry 5.0 will revolutionise smart factory implementation through repetitive process simplification and increased big data analysis through a smarter factory floor plan and workforce.
Do you have a clear SOP, KPI, and knowledge transfer program in hand for 2023?
Sustainable Manufacturing (Circulatory) and Carbon Neutrality
Manufacturing tomorrow requires a more sustainable approach. It’s not just about going green, it’s about making a sustainable process, production and system.
The 60-15 rule of carbon footprint indicates that the manufacturing industry contributes largely to worldwide greenhouse gas emissions – 60% of emissions come from 15% of carbon-intensive utilities (electricity, gas, food, plane, etc.)
Due to the pandemic and reduced economic and social activities in 2020, global carbon dioxide emissions fell by 6.4%, or 2.3 billion tonnes, in 2020. The drastic decrease in air pollution and greenhouse gas emissions shows that after all there may be hope in saving the world. That disaster could be a catalyst.
Through an economic and technical lens, some ways to employ a sustainable manufacturing is as follows:
- Circular manufacturing and economy
Reducing waste by recycling not only end products but also machines, commodities, resources, system, waste, energy, etc.
Circularity refers to a regenerative manufacturing and economic model that encourages manufacturers to use materials and goods repeatedly to prevent quick disposal.
The principle is circularity regulates around elimination of waste and pollution and regenerating nature.
- Plan a 3 and 15 years of sustainable environmental, social, and corporate governance (ESG) plan and use/produce go-green products.
How well can you reduce and reuse natural resources and minimie material, machine, and energy usage?
Eco-friendly products, systems, and/or waste is a good way to establish sustainable manufacturing.
- Carbon Neutrality
Lastly, transition to renewable energy to reduce emission. Geothermal, solar, biomass, water, wind, and many other natural resources can financially facilitate and incentivise manufacturers.
Logistic and Delivery – Offshore/Onshore
Directly correlated to inflation, increased freight rates still remain despite the relief of travel and courier restrictions. With currency depreciation and increased commodity rate, evaluate and consider changing lanes by onshoring and offshoring.
If the main challenge is through logistics, find onshoring options with reasonable commodity prices.
If the main challenge is commodity rate, consider offshoring with a reliable multi-lane logistics and delivery partner.
Whether it is factory closures, rising labor and freight costs, increased fuel price, yet demand; labor shortages, inventory control challenges or lack of warehouse spaces, there is always a solution.
Conclusion
Evaluate your company’s biggest challenge in 2022 prior to evaluating this year’s plan.
- Do you have an automation system in place to overcome your main challenge – efficiency and productivity?
- Do you have a solid structure and foundation of frontline workers, and what process can be made easier and faster with automation? (Prioritise removing paper and pen, digitising, and increased transparency, faster coordination and better management)
- Do you have enough skilled engineers to operate your automation system?
- What is your low-carbon or carbon-neutral manufacturing system?
- Do you have a good employment attraction and retention program?
- Do you have a trusted automation partner to integrate and run your legacy system with a more efficient and effective system?
Ti2 Pty Ltd offer a wide range of quality industrial automotive, automation, and information products and services. Using genuine open standards and technologies for industrial solutions we are able to reduce overall cost of ownership.
To learn more about what we do and how we can help your automation requirements, please click projects, products & services.
Ti2 is currently very focused on working with its global partners to secure stock and avoid long delay times in delivering products to their customers. Together with our trusted partners, we are here to provide solutions.
Please click here to email us your inquiry, we would like to hear from you.