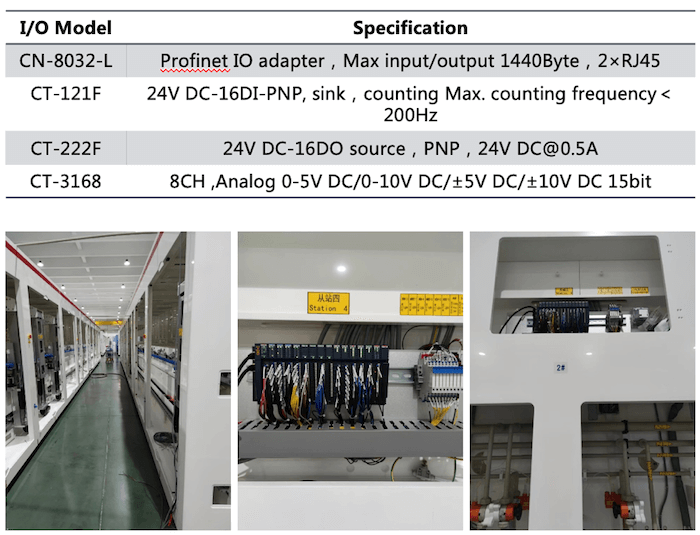
Photovoltaic silicon material plays a critical role in converting solar energy into electricity.
In the world of photovoltaic (PV) technology, the quality and purity of silicon material used in solar panels are of utmost importance. However, ensuring the efficiency and reliability of the photovoltaic silicon material cleaning process is no easy feat. This process involves the removal of impurities and contaminants, which can significantly affect the efficiency and durability of the panels. This is where communication control comes into play.
Effective communication control helps prevent contamination and ensures that the cleaning process is efficient and precise. In this article, we will explore the importance of communication control in photovoltaic silicon material cleaning processes. We will also highlight some of the key factors that contribute to effective communication control and how they can help improve the efficiency and reliability of your photovoltaic silicon material cleaning process.
Silicon material cleaning is an indispensable part of the process of preparing high-purity polysilicon material. Its main function is to clean away the pollutants, metal ions, oxides, etc. attached to the surface of the silicon material to ensure the cleanliness of the silicon material surface. This process requires a high level of automation. At present, most photovoltaic companies have introduced fully automatic silicon material cleaning machines to ensure the quality of silicon materials and improve production efficiency.
Whether you are a professional in the solar energy industry or simply interested in the topic, read on to learn more about the critical role of automation in photovoltaic silicon material cleaning.
The Role of Automation in the Cleaning Process
Automation has become a crucial part of the cleaning process for photovoltaic silicon material. In recent years, advancements in technology have made it possible to automate various stages of the cleaning process, from the initial inspection of the surface to the application of cleaning agents. Automation has several benefits, such as reducing the risk of contamination, improving cleaning efficiency, and reducing labour costs.
One of the most significant advantages of automation in the cleaning process is the ability to control the cleaning process with greater precision. With automation, cleaning agents can be applied with greater accuracy, reducing the likelihood of damage to the surface of the photovoltaic silicon material. Additionally, automation can help reduce the amount of time required to clean photovoltaic silicon material, which can help increase productivity and reduce costs.
Another benefit of automation is the ability to collect data and optimise the cleaning process. With automation, data can be collected in real-time, allowing for immediate adjustments to the cleaning process. This can help improve the overall efficiency of the cleaning process, leading to higher yields and lower costs.
In a well-known photovoltaic equipment company, more than ten silicon material cleaning production lines in a single workshop was using the control combination of Siemens S7-1500 PLC and ODOT CN-8032-L adapter, within control communication through the Profinet protocol.
The ODOT C series IO CT-121F can collect digital input signals such as on-site photoelectric sensors, liquid level sensors, and button switches, and transmit them to the controller through the Profinet protocol.
This allowed the execution of digital output signals from starting actuators (cylinders, valves, etc.), indicator lights, lighthouses, etc. In addition, the controller was able to apply precise temperature control through the ODOT CT-4154 analogue output module. This as a result provided the entire silicon material cleaning production line with a completely efficient and accurate process.
The entire production line uses S7-1500 PLC as the master, ODOT C series distributed IO, V90 servo drive system, and G120 frequency conversion system as the slave station. The slave station is controlled by a distributed IO to control input and output. ODOT prides itself on precise, high-speed, and stable execution in this case study.
Learn more about their IO module HERE.
Benefits of Automation in the Cleaning Process
There are several benefits to using automation in the cleaning process for photovoltaic silicon material. One of the most significant advantages is the ability to reduce the risk of contamination. Contamination can occur at any stage of the cleaning process, from the initial inspection to the final application of cleaning agents. By automating the cleaning process, the risk of contamination can be significantly reduced, helping to ensure that the photovoltaic silicon material remains clean and efficient.
Another benefit of automation is the ability to improve the efficiency of the cleaning process. With automation, the cleaning process can be completed more quickly and accurately, reducing the amount of time and resources required to clean photovoltaic silicon material. This can help increase productivity and reduce costs, leading to higher yields and greater profitability.
Finally, automation can help reduce labour costs. With automation, less labour is required to complete the cleaning process, leading to lower labour costs and increased profitability. Additionally, automation can help reduce the risk of human error, leading to greater consistency in the cleaning process.
Types of Automation Used in the Cleaning Process
There are several types of automation used in the cleaning process for photovoltaic silicon material. One of the most common types is robotic automation, which involves the use of robots to clean photovoltaic silicon material. Robotic automation can be highly effective, as it allows for precise control over the cleaning process while reducing contamination risks.
Another type of automation used in the cleaning process is the use of sensors and monitoring systems. Sensors and monitoring systems can be used to collect data in real time, allowing for immediate adjustments to the cleaning process. This can help improve overall efficiency.
Case Studies of Successful Implementation of Automated Cleaning Process in the Industry
Several companies in the solar energy industry have successfully implemented automated cleaning processes for photovoltaic silicon material. One of the most successful examples is First Solar, a leading manufacturer of photovoltaic silicon material. First Solar has implemented a fully automated cleaning process, which has helped reduce costs and increase efficiency.
Another successful example is SunPower, a leading manufacturer of solar panels. SunPower has implemented a robotic cleaning system that has helped reduce the risk of contamination and improve the overall efficiency of the cleaning process.
Cost-Benefit Analysis of Automation in the Cleaning Process
There are several factors to consider when conducting a cost-benefit analysis of automation in the cleaning process for photovoltaic silicon material. One of the most significant factors is the initial cost of implementing automation. While automation can help reduce costs in the long term, the initial cost of implementing automation can be high.
Another factor to consider is the potential benefits of automation, such as increased efficiency and reduced labour costs. These benefits can help offset the initial cost of implementing automation, leading to higher profitability in the long term.
Finally, it is important to consider the potential risks of implementing automation, such as the risk of malfunction or the need for maintenance. These risks can impact the overall cost-effectiveness of automation and should be carefully considered when conducting a cost-benefit analysis.
ODOT Automation, with extensive experience in the renewable energy industry, can help you assess and identify what cost, system, and processes will best suit your Solar PV silicon application. Click HERE to inquire more and receive a cost analysis.
Future Trends and Developments in Automation for Photovoltaic Silicon Material Cleaning Process
In the future, we can expect to see continued advancements in automation for the cleaning process of photovoltaic silicon material. One potential trend is the use of artificial intelligence and machine learning to optimise the cleaning process. With artificial intelligence and machine learning, the cleaning process can be optimised in real-time, leading to greater efficiency and higher yields.
Overall, communication control is critical in the cleaning process for photovoltaic silicon material. Automation can help improve communication control, leading to greater efficiency and higher yields. While there are challenges associated with implementing automation, the potential benefits, such as reduced labour costs and increased profitability, make it an attractive option for companies in the solar energy industry. As technology continues to evolve, we can expect to see continued advancements in automation for the cleaning process of photovoltaic silicon material.
Ti2 Pty Ltd is the official distributor for ODOT in Australia, offering automation products with expertise from world-class suppliers. We provide robust competitive industrial automation solutions helping manufacturing companies among other emerging industries.
To learn more about what we do and how we can help your interoperability requirements, please click projects, products & services.
Ti2 is currently very focused on working with its global partners to secure stock and avoid long delay times in delivering products to their customers. Together with our trusted partners, we are here to provide solutions.
Please click here to email us your inquiry, we would like to hear from you.